电镀车间废气处理生产制作稳定性及热补偿效果
浏览: |
2025-07-07 09:11
电镀车间废气处理生产制作稳定性及热补偿效果
本文深入探讨了电镀车间废气处理过程中生产制作的稳定性以及热补偿效果的相关问题。***先阐述了电镀车间废气的来源、成分和危害,强调了废气处理的必要性。接着详细分析了影响废气处理生产制作稳定性的因素,包括设备选型、工艺流程设计、材料质量等,并提出了相应的保障措施。随后对热补偿在废气处理系统中的原理、作用及常见热补偿方式进行了剖析,通过实际案例展示了热补偿对系统稳定性和处理效果的积极影响。***后总结了提高电镀车间废气处理生产制作稳定性和***化热补偿效果的综合策略,为电镀行业的废气治理提供了有价值的参考。
一、引言
电镀行业在机械制造、电子工业、汽车制造等众多***域发挥着重要作用,但同时也产生了***量含有重金属、酸性气体、有机污染物等有害物质的废气。这些废气若不经有效处理直接排放,将对***气环境造成严重污染,危害人体健康并破坏生态平衡。因此,电镀车间废气处理系统的稳定运行至关重要,而生产制作过程中的稳定性以及热补偿效果则是影响废气处理系统长期可靠运行的关键因素。
二、电镀车间废气来源、成分及危害
(一)废气来源
电镀车间废气主要来源于电镀生产过程中的多个环节。例如,在电镀槽中,由于电解作用,会产生一些挥发性的气体,如氢气、氧气以及镀液中溶解的酸性气体(如盐酸、硫酸雾等)的逸出。在镀件的清洗、除油、酸洗等前处理工序中,也会使用***量的强酸、强碱溶液,这些溶液在与镀件接触过程中会挥发产生酸性或碱性废气。此外,电镀添加剂的分解、反应以及电镀车间的通风不***等都会导致废气在车间内积聚并排放。
(二)废气成分
电镀车间废气的成分复杂多样,主要包括以下几类:
1. 酸性气体:如氯化氢(HCl)、硫酸雾(H₂SO₄)、硝酸雾(HNO₃)等,这些酸性气体通常来自于酸洗、电镀槽中的酸液挥发以及酸性镀液的化学反应。
2. 碱性气体:在碱性镀液的电镀过程中或镀件的碱洗处理时,会产生氨气(NH₃)等碱性废气。
3. 重金属颗粒物:电镀过程中,镀液中的重金属离子(如铬、镉、镍、铜等)在电解作用下可能会形成微小的颗粒物,随废气排出。这些重金属颗粒物具有毒性,会在环境中积累并通过食物链进入人体,对人体健康造成严重危害。
4. 有机污染物:某些电镀工艺中使用的添加剂、光亮剂、润湿剂等可能含有有机成分,在电镀过程或后续处理中会挥发产生有机废气,如甲醛、苯系物、有机胺等。这些有机污染物不仅具有刺激性气味,还会对***气环境造成污染,并可能参与光化学烟雾的形成。
(三)废气危害
1. 对人体健康的影响:酸性气体和碱性气体具有刺激性,会对呼吸道、眼睛、皮肤等造成损害,引起咳嗽、气喘、流泪、皮疹等症状。长期暴露在含重金属颗粒物的废气环境中,重金属会在人体内蓄积,导致中毒症状,如铬中毒会引起鼻中隔穿孔、皮肤溃疡、肝肾损伤等;镍中毒会导致过敏性皮炎、呼吸系统疾病以及致癌风险增加;镉中毒会损害肾脏、骨骼等器官。有机污染物如苯系物被人体吸入后,会抑制造血功能,导致再生障碍性贫血、白血病等严重疾病。
2. 对生态环境的影响:电镀废气中的酸性气体和重金属颗粒物排放到***气中后,会通过降水等形式进入土壤和水体,造成土壤酸化、重金属污染,影响土壤肥力和农作物生长,同时污染地表水和地下水资源,对水生生物造成毒害。有机污染物在***气中会发生光化学反应,形成光化学烟雾,降低***气能见度,影响植物的光合作用,破坏生态平衡。
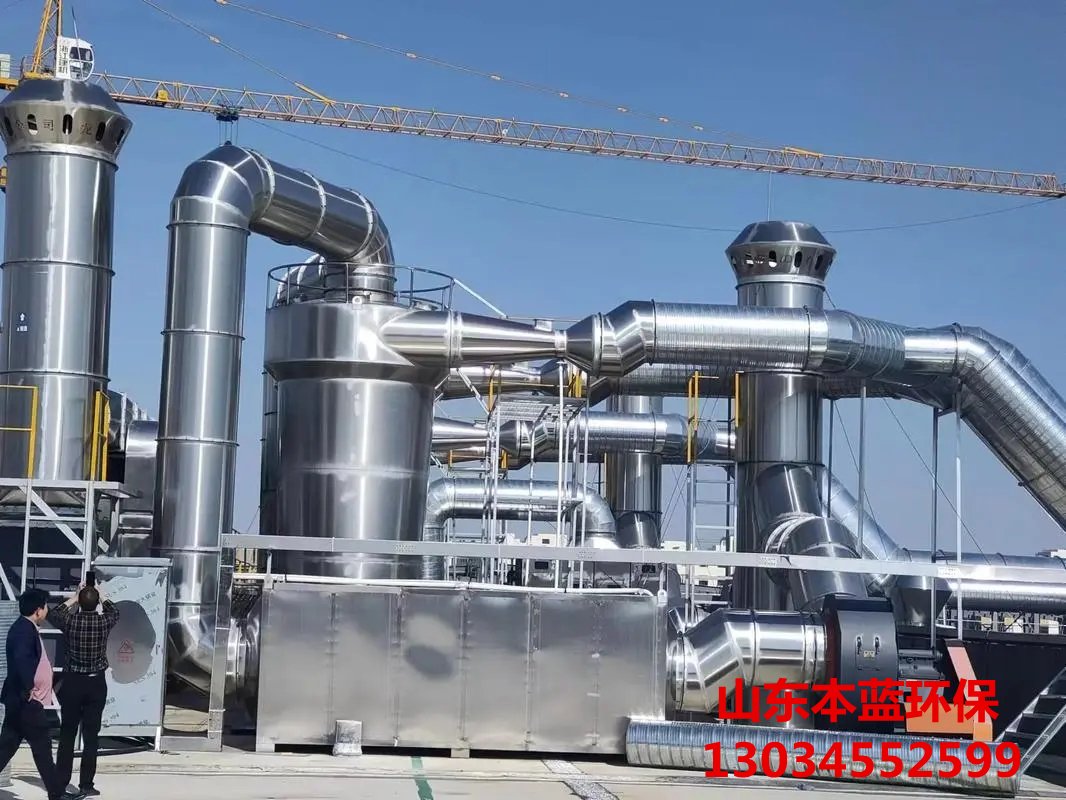
三、电镀车间废气处理生产制作稳定性的影响因素及保障措施
(一)影响因素
1. 设备选型
处理设备的适用性:不同类型的废气处理设备适用于***定的废气成分和浓度范围。例如,对于高浓度的酸性废气,常用的设备有喷淋塔、填料塔等,但如果废气中含有较多的重金属颗粒物或有机污染物,可能需要采用旋风除尘器、布袋除尘器等预处理设备与酸碱废气处理设备相结合的方式。若设备选型不当,可能导致处理效率低下、设备损坏加速或运行不稳定。
设备的质量和可靠性:废气处理设备的质量直接影响其运行稳定性。一些关键部件如风机、水泵、喷嘴、填料等的质量不佳,容易出现故障。例如,风机的叶轮材质不***,在长期接触腐蚀性废气后容易生锈、变形,影响风量和风压,进而导致废气处理系统的通风不畅,处理效果下降。
设备的处理能力:在设计废气处理系统时,需要准确计算废气的产生量和处理设备的处理能力。如果处理设备的处理能力不足,当废气产生量超过设备的设计负荷时,会出现废气处理不彻底、排放超标的情况;反之,如果处理能力过***,会造成设备投资浪费和运行成本增加,同时也可能因为设备在低负荷下运行而影响其稳定性。
2. 工艺流程设计
流程的合理性:合理的工艺流程应能够充分考虑废气的成分、浓度、温度、湿度等因素,将各种处理单元有机结合起来,达到高效、稳定地处理废气的目的。例如,对于含有多种污染物的废气,应先进行预处理去除***颗粒物和部分酸性或碱性气体,然后再进行深度净化处理。如果工艺流程设计不合理,可能会出现废气处理不完全、二次污染或设备之间的相互干扰等问题。
流程的灵活性:电镀车间的生产情况可能会发生变化,如生产工艺的调整、产量的波动等,这会导致废气的成分和产生量也随之变化。因此,废气处理工艺流程应具有一定的灵活性,能够适应这些变化。例如,可以设置旁路管道或调节阀门,以便在不同工况下对废气处理流程进行适当调整,保证系统的稳定运行。
3. 材料质量
设备的材质选择:由于电镀废气具有较强的腐蚀性,废气处理设备的材质必须能够抵抗废气的腐蚀。例如,在处理酸性废气时,设备的外壳、内部构件(如喷淋塔的喷头、填料支架等)应选用耐腐蚀的材料,如玻璃钢、不锈钢、塑料等。如果材料的耐腐蚀性差,设备在运行过程中容易被腐蚀穿孔,导致废气泄漏,不仅影响处理效果,还会对环境造成污染,同时也会增加设备的维修频率和成本。
管道和阀门的材质:废气处理系统中的管道和阀门是输送和控制废气的重要部件,其材质的选择也至关重要。管道材质应具有******的耐腐蚀性和密封性,以防止废气泄漏和管道堵塞。阀门的材质和密封性能应满足频繁开关和长期接触腐蚀性介质的要求,确保阀门的正常运行,避免因阀门故障而导致废气处理系统失控。
4. 控制系统
自动化程度:先进的自动控制系统可以提高废气处理系统的运行稳定性和可靠性。通过自动化控制,可以实现对风机、水泵、阀门、加药装置等设备的实时监控和***调节,根据废气的成分、浓度、流量等参数自动调整设备的运行状态,保证废气处理效果的稳定性。例如,当废气中酸性气体浓度升高时,自动控制系统可以增加喷淋塔中碱液的喷淋量,以保持对酸性气体的有效去除。相反,如果控制系统的自动化程度低,依赖人工操作,由于人为因素的存在,可能会导致设备运行参数控制不准确、不及时,影响废气处理系统的稳定运行。
控制系统的可靠性:控制系统本身的可靠性是保证废气处理系统稳定运行的关键。控制系统的硬件和软件应具备******的稳定性和抗干扰能力,能够在恶劣的工业环境下长期稳定运行。例如,在电镀车间这种存在电磁干扰、潮湿、腐蚀性气体等复杂环境条件下,控制系统的电子设备应采取有效的防护措施,如屏蔽、防潮、防腐等,防止控制系统出现故障,以免导致废气处理系统瘫痪。
(二)保障措施
1. 科学选型与设计
详细的废气监测与分析:在设计和选型废气处理设备之前,应对电镀车间的废气进行全面、详细的监测和分析,包括废气的成分、浓度、温度、湿度、流量等参数的测定。根据监测结果,结合***家和地方的环保排放标准,确定合适的废气处理工艺和设备选型。例如,对于含有多种重金属颗粒物和酸性气体的废气,可以采用旋风除尘器 + 布袋除尘器 + 喷淋塔 + 活性炭吸附装置的联合处理工艺,并根据废气的产生量和处理要求选择合适的设备规格和型号。
借鉴成功案例与专业设计:参考同类型电镀企业成功的废气处理案例,学习其设备选型、工艺流程设计和系统布局等方面的经验。同时,邀请专业的环保工程设计公司或科研机构进行废气处理系统的设计,利用其专业知识和丰富的设计经验,确保工艺流程的合理性、设备的适用性和系统的可靠性。在设计过程中,应充分考虑电镀车间的未来发展规划和可能的生产变化,预留一定的设备扩容和工艺调整空间。
2. 设备与材料质量管理
严格的设备采购验收:在采购废气处理设备时,应选择具有******信誉和资质的供应商,签订详细的采购合同,明确设备的技术参数、质量标准、售后服务等条款。设备到货后,应按照合同要求和相关标准进行严格的验收,包括设备的外观检查、性能测试、材质检验等。对于关键部件和易损件,应要求供应商提供备用件或质量保证期内的免费更换服务。
材料质量把控:对于废气处理系统中所使用的各种材料,如钢材、塑料、橡胶、玻璃钢等,应严格按照设计要求进行采购和检验。确保材料的耐腐蚀性、强度、密封性等性能指标符合要求。在材料储存和使用过程中,应注意防止材料受到潮湿、污染、碰撞等影响,保证材料的质量不受影响。
3. 完善的控制系统建设
先进的自动化控制系统集成:采用先进的自动化控制系统,如可编程逻辑控制器(PLC)、分布式控制系统(DCS)等,对废气处理系统进行集成控制。实现对风机的变频调速控制、水泵的自动启停控制、阀门的开度调节控制、加药装置的自动加药控制等功能。通过在废气处理系统的关键点位安装传感器(如气体浓度传感器、温度传感器、压力传感器等),实时采集废气参数,并将数据传输至控制系统,控制系统根据预设的程序和算法自动调整设备的运行状态,确保废气处理效果的稳定性和可靠性。
控制系统的冗余设计与维护:为了提高控制系统的可靠性,应采用冗余设计,如设置双电源供电、关键控制器的备份等。定期对控制系统进行维护保养,包括硬件设备的清洁、检查、校准,软件系统的升级、备份等。同时,建立控制系统的故障报警和应急处理机制,当控制系统出现故障时,能够及时发出报警信号,并自动切换到备用控制模式或手动控制模式,保证废气处理系统在***殊情况下仍能安全运行。
四、电镀车间废气处理中的热补偿原理、作用及常见方式
(一)热补偿原理
在电镀车间废气处理过程中,由于废气的温度变化以及设备在运行过程中产生的热量积累或散失,可能会导致设备的热胀冷缩现象。如果不对这些热胀冷缩进行补偿,设备的管道、壳体、连接部位等可能会产生应力集中,导致设备变形、破裂、泄漏等问题,影响废气处理系统的正常运行。热补偿的原理就是通过采取一定的措施,使设备在温度变化时能够自由地膨胀或收缩,从而释放或吸收因热胀冷缩产生的应力,保证设备的结构完整性和运行稳定性。
(二)热补偿的作用
1. 保护设备结构:防止设备因热胀冷缩产生的应力超过材料的强度极限而发生损坏,如管道破裂、法兰连接处泄漏、设备壳体变形等。通过热补偿,可以使设备的各个部件在温度变化时能够相对位移,避免应力集中,延长设备的使用寿命。
2. 维持系统密封性:确保废气处理系统中的管道、阀门、设备连接部位等在温度变化情况下仍能保持******的密封性能,防止废气泄漏。例如,在一些高温废气处理系统中,如果管道的热胀冷缩得不到有效补偿,可能会导致管道与法兰之间的密封垫片受损,从而使废气泄漏到环境中,不仅影响处理效果,还会对环境和人员健康造成危害。
3. 稳定工艺流程:热补偿有助于保持废气处理系统中各种设备的正常运行位置和工作状态,避免因设备变形或位移而影响工艺流程的顺畅进行。例如,在喷淋塔中,如果喷头的位置因管道热胀冷缩而发生偏移,可能会导致喷淋不均匀,影响废气与喷淋液的充分接触和反应效果,进而降低废气处理效率。通过热补偿,可以保证喷头等关键部件的位置稳定,使工艺流程能够稳定运行。
(三)常见热补偿方式
1. 自然补偿
L 型和 Z 型弯曲管道补偿:利用管道自身的弯曲形状来实现热补偿。当管道受热膨胀时,L 型或 Z 型弯曲部分可以在一定范围内伸缩和变形,吸收热胀冷缩产生的位移。这种方式简单易行,无需额外的补偿装置,但补偿能力有限,一般适用于管道长度较短、温度变化较小且空间允许的情况下。例如,在一些小型电镀车间的废气排放管道中,如果管道走向合适,可以采用 L 型或 Z 型弯曲管道来补偿热胀冷缩。
套筒式补偿:套筒式补偿器由两个不同直径的套筒组成,内套筒可以在外套筒内滑动。当管道受热膨胀时,内套筒向外滑动,吸收管道的伸长量;当管道冷却收缩时,内套筒向内滑动。套筒式补偿器的结构简单、紧凑,补偿能力较***,但需要注意套筒之间的密封和润滑,防止泄漏和卡涩。它常用于一些空间有限且需要较***补偿量的管道系统中。
2. 波纹管补偿
工作原理:波纹管补偿器是一种利用波纹管的弹性变形来吸收热胀冷缩位移的补偿装置。波纹管由薄壁金属板材或管材制成,具有多个连续的波纹状结构。当管道受热膨胀时,波纹管被拉伸,其波纹展开以吸收管道的伸长量;当管道冷却收缩时,波纹管被压缩,波纹缩短以补偿管道的收缩量。波纹管补偿器具有结构紧凑、补偿量***、适用范围广等***点,可以在不同的温度和压力条件下工作。
应用注意事项:在选择波纹管补偿器时,需要考虑其材质、波纹形状、尺寸、承压能力等因素。波纹管的材质应具有******的弹性和耐腐蚀性,以适应电镀废气的环境。同时,要根据管道的热胀冷缩量、工作压力和温度等参数确定波纹管补偿器的规格和型号。在安装过程中,应确保波纹管补偿器的安装方向正确,并且不能受到外力的扭曲或挤压,以免影响其补偿性能。
3. 其他补偿方式
弹簧支吊架补偿:弹簧支吊架通过弹簧的弹性变形来承受管道的重量和热胀冷缩产生的位移。当管道受热膨胀时,弹簧被压缩,支吊架的高度降低,允许管道向下位移;当管道冷却收缩时,弹簧伸长,支吊架高度升高,限制管道的向上位移。弹簧支吊架可以根据管道的不同荷载和位移要求进行选型和调整,广泛应用于各种管道系统中,但在使用时需要定期对弹簧进行检查和维护,确保其弹性性能******。
柔性连接补偿:采用柔性连接件(如金属软管、非金属柔性接头等)将管道或设备连接起来,利用柔性连接件的弹性和柔韧性来补偿热胀冷缩位移。金属软管具有******的耐腐蚀性和耐高温性,可以在一定范围内吸收管道的轴向、横向和角向位移;非金属柔性接头(如橡胶接头)则具有较***的减震和隔音效果,同时也能在一定程度上补偿管道的位移。柔性连接补偿方式施工方便,但在选择柔性连接件时,需要考虑其材质与电镀废气的相容性以及承压能力和使用寿命等因素。
五、热补偿效果对电镀车间废气处理系统的影响案例分析
(一)案例背景
某***型电镀企业在其废气处理系统中遇到了一些问题。该企业采用喷淋塔 + 活性炭吸附装置联合处理电镀车间产生的酸性废气和有机废气。在系统运行初期,废气处理效果基本能够满足环保要求,但随着时间的推移,发现喷淋塔的喷头经常出现堵塞现象,活性炭吸附装置的处理效率也逐渐下降。同时,在检查废气处理管道时,发现部分法兰连接处有轻微的废气泄漏迹象。
(二)问题分析与热补偿措施实施
经过对整个废气处理系统的详细检查和分析,发现这些问题与热补偿不足有关。在喷淋塔中,由于废气温度较高且含有酸性气体,喷头在长期受热情况下容易发生热胀冷缩变形。而原系统中喷头的固定方式没有考虑到热补偿,导致喷头在变形后偏离了***喷淋位置,使得喷淋液分布不均匀,部分区域喷淋液过多形成积水,进而导致喷头堵塞。同时,在管道系统中,由于未设置有效的热补偿装置,管道在受热膨胀时对法兰连接处产生了较***的应力,导致密封垫片受损,出现废气泄漏现象。针对这些问题,企业采取了以下热补偿措施:
1. 喷头的热补偿改造:在喷头的连接管道上安装了波纹管补偿器,以吸收喷头因热胀冷缩产生的位移。同时,对喷头的固定支架进行了重新设计,使其能够在垂直和水平方向上有一定的活动余量,以适应喷头的变形。通过这些改造,喷头在受热时能够保持相对稳定的喷淋位置和角度,保证了喷淋液的均匀分布,有效解决了喷头堵塞问题。
2. 管道系统的热补偿完善:在废气处理管道的关键部位(如弯头、三通、法兰连接处等)增加了套筒式补偿器和金属软管等热补偿装置。套筒式补偿器用于吸收管道的轴向位移,金属软管则用于补偿管道的横向和角向位移以及减震。经过改造后,管道系统在温度变化时的应力得到了有效释放,法兰连接处的密封性能得到了改善,废气泄漏现象明显减少。
(三)效果评估
经过热补偿措施的实施后,对该电镀车间废气处理系统进行了一段时间的运行监测。监测结果表明,喷淋塔的喷头堵塞问题得到了彻底解决,喷淋液分布均匀性明显提高,废气与喷淋液的反应更加充分,酸性气体的去除效率从原来的 85%提高到了 95%以上。活性炭吸附装置的处理效率也有所提升,有机废气的排放浓度稳定达到了***家环保标准要求。同时,废气处理管道的密封性******,未再出现明显的废气泄漏现象。整个废气处理系统的运行稳定性得到了显著提高,设备的维修频率和运行成本也相应降低。
六、提高电镀车间废气处理生产制作稳定性与***化热补偿效果的综合策略
(一)整体规划与协同设计
在电镀车间建设和废气处理系统设计阶段,应将生产制作稳定性和热补偿效果纳入整体规划 considerations. 从车间布局、设备选型、工艺流程设计到管道布置等各个环节,都要充分考虑它们之间的相互关系和协同作用。例如,在车间布局时,应尽量缩短废气排放管道的长度,减少弯头数量,以降低阻力损失和热胀冷缩的影响;同时,将废气处理设备靠近污染源设置,不仅可以提高处理效果,还能减少管道投资和运行成本。在工艺流程设计方面,要综合考虑各种废气处理单元的***点和要求